How To Set Up A Lincoln Stick Welder
I was e'er struggling with how to properly hook upward stick welding leads to the welder. Should you connect the footing lead to the welder's negative terminal or the positive one? Where should the electrode lead go? Ane tin can just make things as complicated as he wants.
Many people become confused while agreement the connections of a stick welder. But allow me tell you, later on I realized that information technology is not as complex equally it seems.
You can connect the welding leads in three different ways called the DCEN connectedness, DCEP connection, and the Air-conditioning connection. Each connection has its pros and cons. They should be changed co-ordinate to the welding application they are beingness used in.
In this commodity, I will discuss in detail how to hook up stick welder leads for different welding applications.
Let'southward jump right in.
SMAW or stick welding
Shielded Metal Arc Welding, normally known as stick welding is the most popular form of arc welding. Information technology uses electric electric current (usually DC) to melt both the metal workpiece and the electrode rod, forming a weld pool. The electrode is covered with a layer of flux which protects the molten weld from being contaminated by foreign particles (that's why it's chosen Shielded Metal Arc Welding).
Stick welding setup
Stick welding setup consists of the following equipment:
- A welding automobile
- Welding leads (Piece of work Cables)
- Electrode holder
- Ground clamp (Work Clamp)
- Welding rod (Electrode)
The diagram below shows these components in their proper organisation.

What are leads on a welder?
Welding leads or welding cables, just similar other copper wires, are electric conductors wrapped inside an insulating rubber jacket. These cables come up in different diameters and lengths. For loftier current applications, we use cables with a large diameter equally they offering less resistance to the electric current. Similarly, for low current applications, you tin use the ones with a smaller diameter. It all just comes to the nature of your application.
You accept two types of welding leads in stick welding: The electrode lead and the work lead (likewise chosen the ground lead). Electrode lead connects our welding machine to the electrode holder. Similarly, the ground lead hooks it up to the workpiece.
Determining welding lead sizes.
Welding leads come in different sizes. While hooking upwards stick welding leads, you should be extremely conscious about their size. If your cablevision selection is incorrect, yous won't exist able to get the desired current and voltage to the welding arc. Consequently, bug like excessive spatter and lack of fusion can occur. Sometimes, if the amperage falls too low, your stick welder simply won't arc.
The following tabular array shows the correct size of copper and aluminum cables for different stick welding amperage values and lengths of the welding cables.
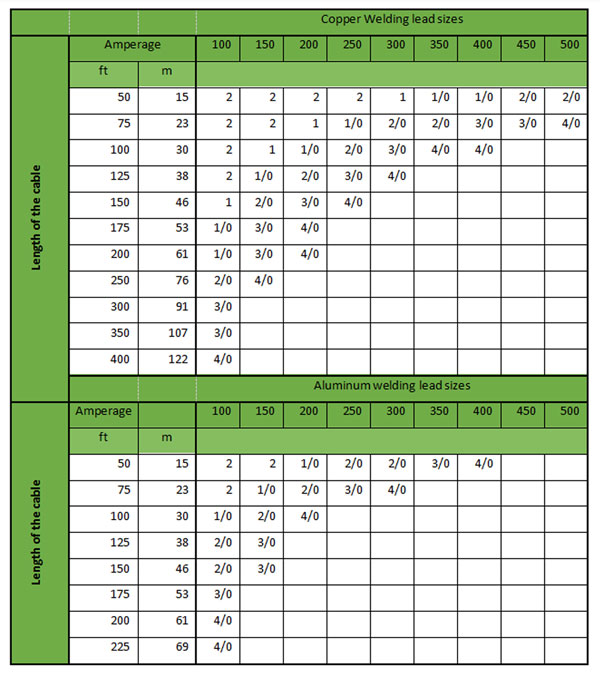
For case, if your workpiece is almost 100 feet away from the welder and your application requires 200 Amps, ask your welding retailer for an aluminum cable of size 4/0 or a copper cablevision of size 1/0.
Steps to fix stick welding leads
To properly connect the stick welding leads, just follow these unproblematic steps
i. Footing clamp placement
First of all, attach the footing clamp at its appropriate position. Ground clamp connects our workpiece to the ground via the work lead. You can either clip it directly to the workpiece or to the metallic tabular array on which your work is to be done (as shown in the figure).
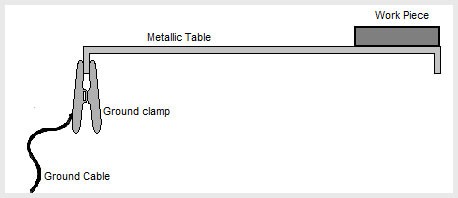
2. Hook upwards welding leads to the welder
After that, adhere the work atomic number 82 to the negative terminal of the welding auto and electrode cable to the positive last. You tin can besides brand connections opposite to this depending upon the welding application. Later in this commodity, I will go to the details of these connections.
Some welding machines have a switch that can be flipped to modify the polarity. Otherwise, y'all have to manually commutation the connections of the welding cables. Earlier you alter the polarity on a welding car, make sure to turn it off.
3. Plug-in the welding machine
Finally, plug in the machine and switch it on. Fix information technology upward to the advisable current and voltage settings every bit per your welding application. You are proficient to go.
Three types of welding setups: DCEN, DCEP, and Ac
Many people ask me whether stick welding is a basis positive or ground negative process. The answer to this question is, "BOTH". In fact, for stick welding, you lot tin can hook upwards the welding cables in three different ways.
1. DCEP welding connectedness
For DCEP or direct current electrode positive connection (formerly known equally reverse polarity), you lot have to connect the electrode holder to the positive concluding and the ground clench to the negative i. As a result, electrons volition flow from the workpiece towards the electrode. For most stick welding applications, nosotros employ the DCEP setup. The diagram below shows the setup for the DCEP connection.
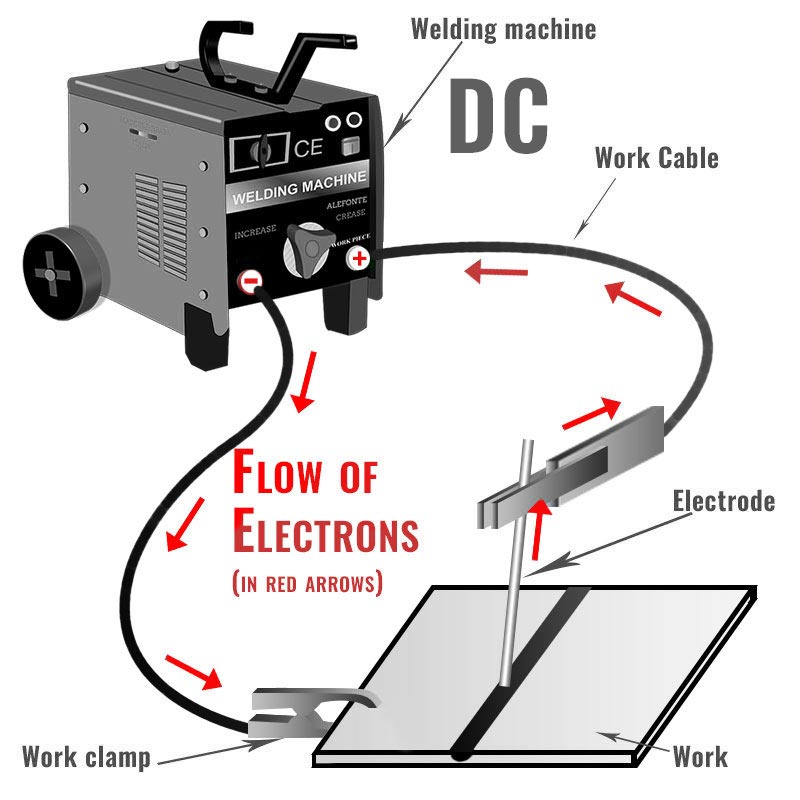
2. DCEN welding connectedness
In DCEN or direct current electrode negative (formerly known as straight polarity), the electrode holder is negative and the workpiece is positive. Hence, electrons menstruation from the electrode towards the positive workpiece. The following figure shows the setup diagram for the DCEN connection.
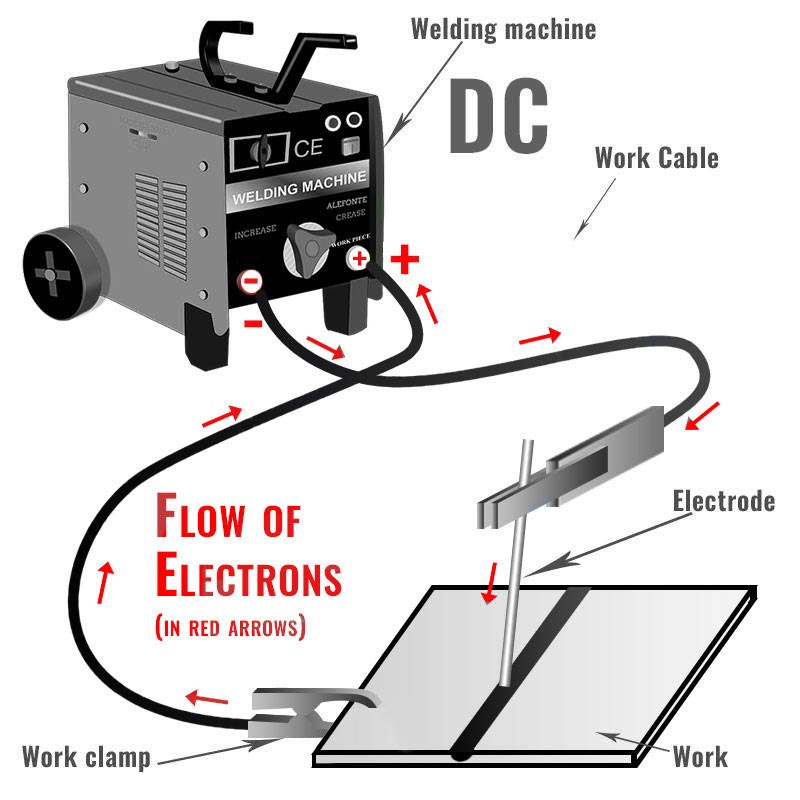
three. Air-conditioning connection
In an Air conditioning welding connection, alternate current usually at a frequency of 60Hz is used. The current changes management every 120thursday role of a 2nd. Therefore, an AC welding connection has no polarity which results in even distribution of heat betwixt the electrode and the workpiece. Post-obit diagram illustrates the setup for Air-conditioning connection.

DCEP vs DCEN: What polarity should you lot stick weld on?
For about of the applications, we hook upwardly the welding leads in a DCEP connectedness. Notwithstanding, stick welding is quite versatile in terms of polarity.
Go on in mind that electrons always travel from the negative terminal of the welder towards the positive terminal. Therefore, in case of DCEP, the electrons leave the surface of the metal and move towards the electrode because the work pb is connected to the welder's negative terminal. These electrons after colliding with the positive electrode produce a large amount of estrus. As a result, almost two-thirds of the welding oestrus generates on the electrode and the remaining one-third of the heat accumulates on the workpiece. On the opposite, for DCEN, two-thirds of the heat is formed on the metal existence welded because the electrons flow from the electrode towards the base of operations metal.
Y'all can not just randomly choose whatsoever welding setup. Each connection has its applications and limitations. As well, not all the electrodes piece of work with both DCEP and DCEN.
DCEP, as I mentioned before, produces high heat on the electrode which results in deep penetration. Withal, the electrode deposition charge per unit in DCEP is low every bit compared to DCEN. Thus, it is not suitable for welding sparse sheets as it may rupture them.
On the other hand, DCEN connection generates less heat on the electrode which provides less penetration. Nevertheless, the filler metal deposition charge per unit is quite high as compared to DCEP. If you lot have to weld thin sheets, I suggest you going for DCEN.
Electrode Selection for different polarities
Different electrodes work best on different current types. Some are good for DC and some for Ac. In fact, it depends a lot on the electrode's coating type. To choose the proper one for your application, the following table might come up in handy.

Arc cleaning action in DCEP
One of the main advantages of DCEP over DCEN is its oxide cleaning action.
During arc welding, it is very of import to make clean the surface of the metal in order to have a good weld. Dirt, rust, oxides and other particles must exist removed. Otherwise, these impurities volition mix with the molten metal and upshot in a weak weld.
In DCEP, the avalanche of electrons moves from the base metal towards the positive electrode. This electron stream breaks the not-conducting oxide layer in the metallic and inherently removes the contaminated particles from the metal resulting in a stiff weld.
Air-conditioning Welding vs DC welding
Almost high power machines run on DC. Some professional TIG and SMAW welders have the power to run on both Air conditioning and DC. But what'southward better, Ac or DC? If more than 90 percent of the times nosotros use DC, why do we even need AC welding?
DC welding is quite polish as compared to Air-conditioning. Have a expect at the post-obit waveform for AC. Each time the polarity switches from positive to negative, there is a moment when the current flowing is nil (run into the scarlet marks). Due to this discontinuous flow of current, the arc formed is quite irregular.
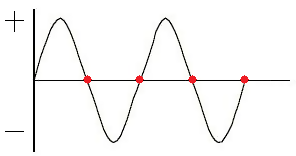
However, in some cases, yous tin prefer Air-conditioning over DC. One major pro of AC is its arc blow emptying capabilities. Are your welds crooked or wavy? Is there too much spatter around your weld? If "aye", your weld might be suffering from arc blow. Switching to AC tin can get rid of such problems. Nonetheless, DC welding has far more than advantages than Air conditioning.
Stick Welding Troubleshooting for Welding Leads
Prevention is always better than cure. Incorrect usage of welding cables can result in problems similar pocket-sized output current, high resistance, and difficulty in starting arc. Therefore, information technology is always better to employ the advisable cables and employ the proper welding technique. Nevertheless, if some complications arise due to the wrong usage of cables, this small troubleshooting guide might aid you do away with these bug.
- Straighten the cables.
- Make certain there are no bends or coils in the cable equally it can cause inductance effects in the wires.
- Lower quality cables tin can cause arc starting problems. Apply high-quality cables.
- Utilise the welding leads of proper size. Run across the tabular array provided above in this commodity.
In Summary,
For most of the stick welding applications, you need to connect your electrode lead to the positive terminal and ground lead to the negative (DCEP connexion). While hooking upwards the welding leads, yous should practise farthermost caution.
In fact, incorrect cable connections can atomic number 82 to issues like poor penetration, poor filler deposition or arc blow problems. But once you lot empathize the cause, the solution seems quite obvious. Best of luck with your welding ventures.
How To Set Up A Lincoln Stick Welder,
Source: https://www.weldingtribe.com/how-to-hook-up-stick-welding-leads/
Posted by: ioriohasold.blogspot.com
0 Response to "How To Set Up A Lincoln Stick Welder"
Post a Comment